PVC Explained: What It Does Well (and Where It Doesn’t Fit)
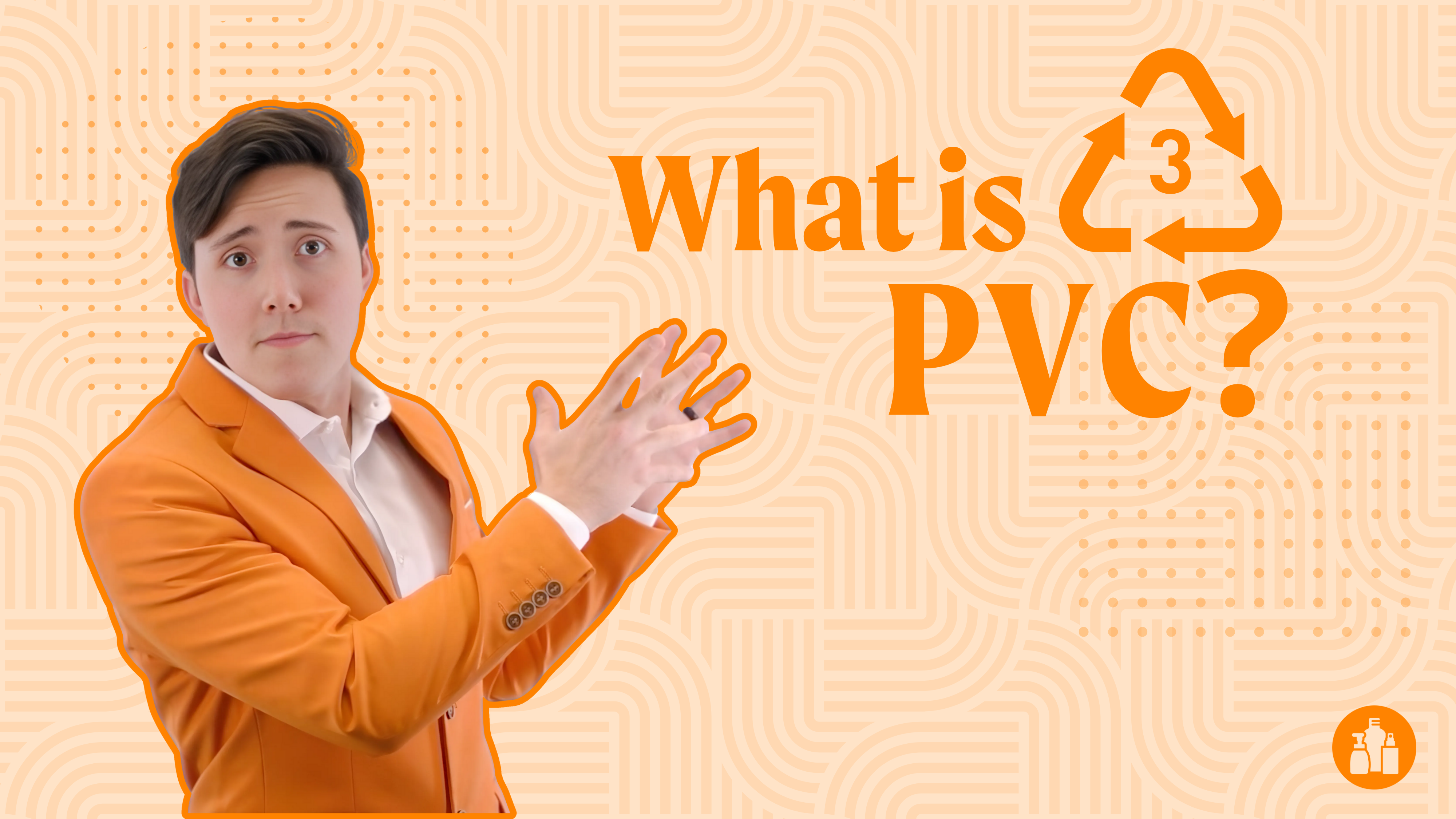
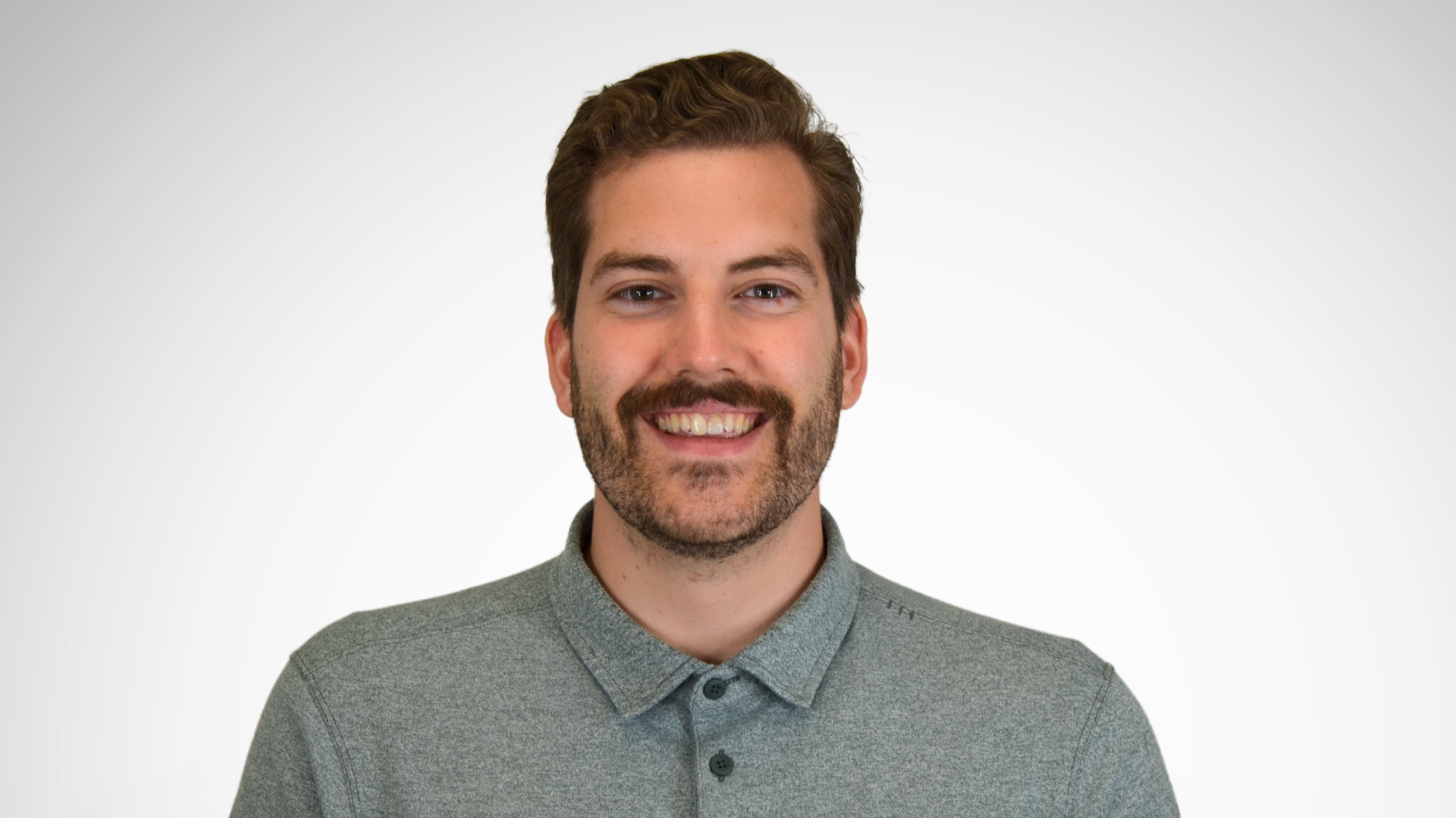
What is PVC (Polyvinyl Chloride)?
You might know PVC as the white piping in your garage or that shrink wrap hugging your energy drink label a little too tightly. It’s that number 3 triangle on the bottom of a container, the mysterious middle child of the plastic family. And while it may not get as much packaging fame as HDPE or PET, this polymer plays a versatile, role in the material world.
Let’s crack into what PVC is, why it’s both loved and avoided, and whether it deserves a spot in your packaging lineup.
PVC: Tough, Transparent, and a Bit Tricky
PVC stands for polyvinyl chloride, a synthetic plastic polymer that’s been a workhorse in industries like construction, plumbing, and healthcare for decades. Why? Because it’s strong, rigid, flame-resistant, and provides excellent insulation against electricity.
You’ll see it in everything from electrical cables and water pipes to window frames and sprinkler systems. It’s like the Swiss Army knife of building materials, but what about packaging?
A Less Common Guest in the Packaging World
PVC can be used in packaging, and sometimes it’s a great fit. But truthfully? It’s not always the top pick.
One major reason: recyclability. Yes, PVC has that triangle symbol with the number 3, but don’t be fooled. Most curbside recycling programs in the U.S. don’t actually recycle PVC. It’s complicated to process and can contaminate other recycling streams.
Still, PVC holds its own in some niche packaging circles thanks to its unique blend of properties.
Why Use PVC in Packaging?
Despite its recyclability issues, PVC brings some pretty cool strengths to the table:
Clarity: PVC has a naturally clear appearance, making it ideal for products that want to show off.
Moderate rigidity and durability: It’s tougher than LDPE but not quite as stiff as HDPE.
Barrier protection: It performs well against oxygen and moisture, which matters if you’re packaging items that are sensitive to the elements.
Chemical resistance: PVC can hold up against alcohols, oils, some acids, and solvents, making it useful for industrial chemicals and medical lab applications.
Shrink compatibility: It’s a go-to for shrink sleeves, shrink bands, and shrink labels thanks to its heat-reactive nature.
Where You’ll Actually See PVC
PVC is still used for a handful of packaging applications:
Dry food containers: Think jerky canisters and oversized snack tubs.
Shrink packaging: Wrapping products securely with clear labeling.
Medical and lab containers: Thanks to its barrier properties and chemical resilience.
Some personal care items: In cases where clarity or rigidity is key.
So... Why Is PVC Falling Out of Favor?
Ah, here’s the catch. Despite its perks, PVC comes with baggage:
Contains BPA: Yep, that controversial additive is often used in PVC, unless the product is labeled as BPA-free (check near the recycle symbol on the bottom).
Recycling limitations: Due to its chemical composition and processing challenges, PVC isn’t commonly accepted in standard recycling programs and can complicate recycling efforts.
Temperature sensitivity: It becomes brittle in the cold (below 32°F) and starts to distort at around 140°F. That makes it a less-than-ideal candidate for hot-fill applications.
Not food or sunlight-friendly: For beverages, wet foods, or products that sit in the sun all day, HDPE or PET are usually safer bets.
Natural Look, Color Options, and Customization
In its raw state, PVC is actually crystal clear. That’s one of its best features. But if you’re going for a custom look, PVC can be made opaque or translucent in nearly any color. Just know that most stock options stick to the classic see-through variety.
PVC vs. The Other Guys
If you’re choosing between PVC and another plastic, here’s how it stacks up:
PVC vs. HDPE: HDPE is more impact-resistant and fully recyclable. PVC offers more clarity but can be brittle and isn’t curbside-recyclable.
PVC vs. PET: PET has better clarity and is safer for consumables. It’s also more widely accepted in recycling. PVC holds up better to certain chemicals but loses on sustainability.
PVC vs. LDPE: LDPE is flexible and soft, ideal for squeeze bottles and plastic bags. PVC is stiffer and more suitable for rigid containers or shrink applications.
PVC vs. PP (Polypropylene): PP is great for hot-fill products and microwave use. PVC, not so much. But PVC wins in clarity and shrink performance.
Should You Use PVC for Your Product?
Here’s a handy gut-check list. PVC might be a fit if:
You need clarity and stiffness in your packaging.
Your product is dry, chemically stable, or doesn’t require cold/hot filling.
You’re using shrink sleeves or bands.
You’re in medical, industrial, or food-safe dry goods territory.
But if your product needs to be ultra-sustainable, recyclable, hot-fillable, or freezer-tolerant, then PET, HDPE, or PP might be better options.
And of course: always test your packaging before committing to a full production run.
Let’s Talk (And Maybe Sample?)
Still unsure if PVC is right for you? Or need to compare samples of PVC, HDPE, and PET side-by-side? We’ve got you covered. Reach out and we’ll help you navigate the material maze like a pro.
Let’s find your perfect plastic match.